Lean Management – Die Methodenauswahl und Geisteshaltung für den Start
Unterstützende Informationen zum Podcast #11 Organisationsentwicklung in einem KMU 1/2 – LEAN MANAGEMENT
Grundsätzlich sollte sich der Methodeneinsatz im Management an dem Reifegrad einer Organisation ausrichten und nicht nach aktuellen „Managementströmungen“. Oft wird mit teilweise sehr komplexen Methoden gearbeitet, ohne allerdings zu prüfen, ob die Methoden zum eigentlichen betrieblichen Problem passen, und ob die Methoden von den Führungskräften und Mitarbeitern verstanden und beherrscht werden. Wird dies nicht beachtet, was eher die Regel ist, so führt der Methodeneinsatz dazu, dass sich Beschäftigte und Führungskräfte aus dem Veränderungsprozess verabschieden und eine mehr oder weniger neutrale Position beziehen. Dies ist insbesondere dann zu beobachten, wenn durch das Top-Management in zeitlich kurzen Abständen unterschiedliche Methoden in den Fokus genommen werden.
Kein Managementsystem, auch nicht Lean Management, sollte daher kampagnenartig über Methoden implementiert werden. Viel wichtiger ist die Erzeugung von Verständnis und Akzeptanz bei Beschäftigten und Führungskräften für den verfolgten Weg in Richtung einer Vision. Das Ziel sollte es sein, dass Verbesserungs- und Veränderungsprozesse nicht aus einem betrieblichen Zwang durchgeführt, sondern vielmehr aus Überzeugung umgesetzt werden. Auf diese Weise kann vermieden werden, dass einzusetzende Methoden letztendlich nicht gelebt werden, und somit kein nachhaltiger Veränderungsprozess herbeigeführt werden kann.
Zu den etablierten Methoden beim Start in Richtung Lean Management zählen in der Regel die Methoden 5A bzw. 5S (Ordnung und Sauberkeit), der Blick für die „7 Arten der Verschwendung“, 5W? und ein einfaches Prozessmanagement. Parallel hierzu sollte auch das Thema „Führung vor Ort“ angegangen werden, um eine Basis für gegebenenfalls komplexere Methoden zu legen. Dies ist insofern wichtig, da sich z.B. an 5A bzw. 5S die Entwicklung von Standards anschließt, die wiederum stabilisiert und weiterentwickelt werden sollten. Erst wenn diese Elemente in der Organisation fest verankert sind, macht es Sinn, über den Einsatz komplexerer Methoden nachzudenken. Bis dieser Reifegrad allerdings in den meisten Unternehmen erreicht ist, vergehen in der Regel Monate bis Jahre.
(Einfaches) Prozessmanagement
Prozessdenken steht immer vor Abteilungsdenken. Am Ende eines Prozesses ist immer ein interner/externer Kunde, dessen Wünsche mit Blick auf Kosten, Lieferzeit, Qualität, Geschwindigkeit usw. zu erfüllen sind.
Die 7 Arten der Verschwendung (7V)
Zu den Grundprinzipien bei Toyota zählt bis zum heutigen Tag die Vermeidung von Verschwendung in den Prozessen. Verschwendung muss kontinuierlich und nachhaltig aus den Arbeitsprozessen im Unternehmen entfernt werden. Der Weg hierzu führt über das Bewusstmachen des sorgfältigen Umganges mit Ressourcen, um den als „Verschwendung“ deklarierten Zeit-, Informations- und Materialaufwand zu erkennen und zu reduzieren. Taiichi Ohno, ehemaliger Produktionschef von Toyota, hat sieben Arten der Verschwendung definiert:
- Überproduktion – produziere, erstelle, schreibe, drucke usw. nur genau das, was auch vom Kunden benötigt wird.
- Bestände – reduziere Materialbestände in der Produktion und Verwaltung
- Transport – vermeide z.B. unnötigen Transport von Material und Informationen, Umschichtungen usw.
- Wartezeiten – vermeide Zeitverschwendung durch Warten, Laufen, Suchen usw.
- Arbeitsprozess – vermeide z.B. unnötige Stillstände, umständliche Arbeitspraktiken, Unterbrechungen einer angefangenen Tätigkeit usw.
- Bewegungen – vermeide unnötige Bewegungen im Arbeitsprozess
- Fehler/Reparaturen – vermeide die Erzeugung und Weiterverwendung von Produkten, Informationen usw. die nicht einwandfrei sind. Denke an den Aufwand für die Reparatur bzw. Nacharbeit und die Kosten von Ausschuss.
Die geschilderten Verschwendungsarten sind oftmals miteinander verknüpft, d.h. eine Verschwendungsart kann wiederum eine andere verursachen. So kann bspw. Überproduktion die Ursache von zu hohen Lagerbeständen sein und diese verursacht überflüssige Bewegungen (Transporte) mit überproduzierten Gütern.
Auch vermeintlich geringfügige Verschwendungen im Prozess können kumuliert große Auswirkungen auf das Betriebsergebnis haben. Ein Beispiel kann dies verdeutlichen: 30 unnötige Schritte, die 20-mal pro Tag gegangen werden und jeweils 15 Sekunden dauern, summieren sich auf 2 Arbeitstage pro Jahr.
5S – Ordnung und Sauberkeit
Die Methodik 5S gilt als Basis vieler Methoden im Lean Management. Sie gilt im Allgemeinen als wenig anspruchsvoll und ist leicht zu erlernen und anzuwenden. Weltweit ist sie in der Regel die Einstiegsmethode beim Themen Lean Management.
Das Ziel der Methodik ist in der Regel die Schaffung von Übersicht und Ordnung an Arbeitsplätzen oder auf Servern, um z.B. Weggleiten und Rüstzeiten zu reduzieren und Suchzeiten zu vermeiden. Darüber hinaus dient sie der Steigerung des Verantwortungsbewusstseins und der Disziplin von Beschäftigten und Führungskräften, der Transparenz von betrieblichen Abläufen, der Arbeitssicherheit, der Qualitätssteigerung durch Fehlervermeidung und ist die Basis u.a. für vorbeugende Instandhaltung und Methoden wie z. B. Total Productive Maintenance und Rüstzeitminimierungen. Die Methodik kann branchenübergreifend und in allen Bereichen eines Unternehmens wie Produktion, Büro usw. angewendet werden.
Viele Fachexperten, Wissenschaftler, Berater und auch Topführungskräfte glauben, dass die 5S-Methode schnell zu implementieren ist und man sich dann den vermeintlich wichtigeren, da anspruchsvolleren Themen und Methoden zuwenden kann. Doch diese Einschätzung ist zumeist ein Trugschluss, der in den USA und in Europa immer noch (zu häufig) anzutreffen ist. Auf der Basis von mehr als 20 Jahren Erfahrung des Autors in der Beratung, Begleitung und Umsetzung von Lean- und „Toyota-Themen“ in Unternehmen diverser Branchen und Größenordnungen, ergänzt um Vor-Ort-Besichtigungen von Unternehmen in Japan und China, lassen sich folgende Feststellungen treffen:
- Wer die 5S-Methode im täglichen betrieblichen Handeln nicht beherrscht, d.h. konsequent, diszipliniert und nachhaltig betreibt, wird an vielen Themen des Lean Managements scheitern oder aber nicht die Erfolge erzielen, die möglich wären.
- Wer glaubt, dass diese Methode kurzfristig und ohne großen Aufwand implementiert werden kann, hat scheinbar weder das notwendige Fachwissen noch einen großen fachlichen Erfahrungsschatz.
- Wer die Meinung vertritt, dass die 5S-Methode keine elementare Führungsaufgabe auf allen Hierarchieebenen ist, da Führungskräfte allgemein wichtigere Themen zu verfolgen haben, sollte sich generell bzgl. des eigenen Führungsverständnisses in diesem Themenfeld hinterfragen.
Bevor nachfolgend auf die Bedeutung von 5S näher eingegangen wird, um die vorhergehenden Aussagen zu unterstützen, erfolgt zunächst ein Überblick über die Methode. Die Methode 5S hat vornehmlich zum Ziel, Übersicht und Ordnung in allen Arbeitsbereichen eines Unternehmens zu erhöhen.
5S steht für die japanischen Begriffe:
Seiri (Sortiere aus):
Im ersten Schritt werden am Arbeitsplatz Arbeitsmittel, Informationen usw., die nicht regelmäßig benötigt werden oder doppelt vorhanden sind, aussortiert.
Seiton (Ordnung schaffen):
Als nächstes werden die am Arbeitsplatz verbliebenen Arbeitsmittel, Informationen usw. sinnvoll angeordnet, z.B. nach Häufigkeit der Benutzung.
Seiso (Säubere):
Anschließend wird der Arbeitsplatz oder der Server gereinigt bzw. „gesäubert“ und ein Rhythmus, in dem die Reinigung wiederholt wird, bestimmt.
Seiketsu (Sauberkeit bewahren):
Um den Zustand von Ordnung und Sauberkeit dauerhaft aufrechterhalten zu können, sollten zur Orientierung entsprechende Standards festgelegt werden.
Shitsuke (Selbstdisziplin üben):
Mit der Zeit schleichen sich gewöhnlich wieder alte Gewohnheiten ein, die dazu führen, dass Ordnung und Sauberkeit am Arbeitsplatz abnehmen. Aus diesem Grund ist es sinnvoll regelmäßig die Schritte eins bis vier zu durchlaufen und ggf. auch die bestehenden Standards weiterzuentwickeln bzw. zu optimieren.
Im deutschen Sprachraum ist neben der Bezeichnung 5S auch 5A gebräuchlich. Die 5A bedeuten hierbei in der Regel:
- Aussortieren,
- Aufräumen,
- Arbeitsplatz sauber halten,
- Anordnung zur Regel machen und
- Alle Schritte wiederholen.
Weitere Bezeichnungen sind in Deutschland oftmals auch „Ordnung und Sauberkeit“, „Rote-Karte-Aktion“ und/oder SOS (Sicherheit, Ordnung, Sauberkeit).
5W? – Frage fünfmal „Warum?“
Die Anwendung der Methodik 5W? (fünfmal „Warum?“: fünfmal hintereinander „Warum?“ zu fragen) ist eine relativ einfache und effiziente Methode für die Suche nach den tatsächlichen Ursachen von Problemen und Abweichungen. Sie gilt als Basis zur Erkennung von Potenzialen und der Erleichterung der täglichen Arbeit. Sie stellt allerdings oftmals die Unternehmenskultur und die abteilungsübergreifende Zusammenarbeit auf eine harte Probe (Siehe Abbildung).
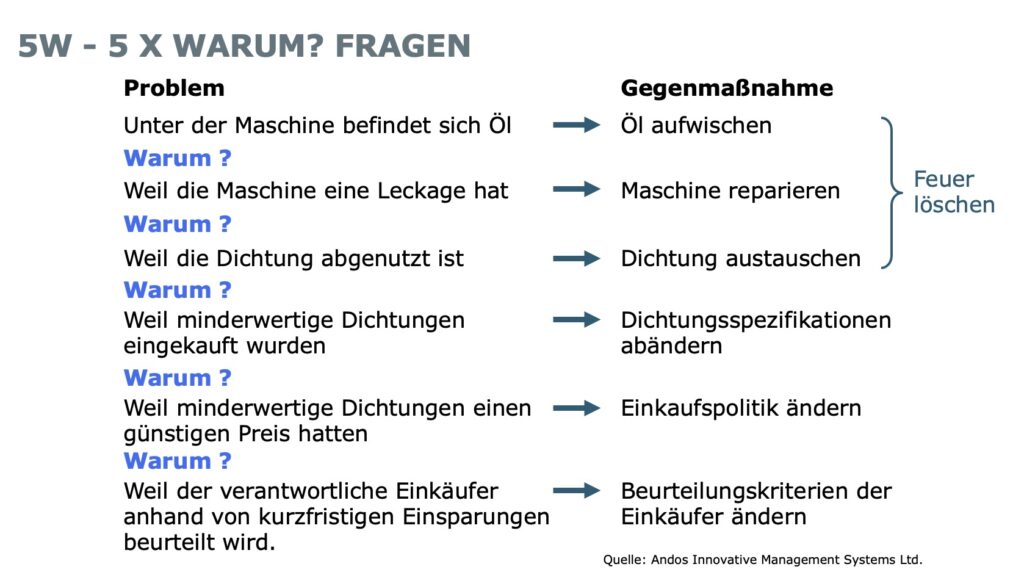
Zusammenfassung
Die größte Herausforderung bei den geschilderten Methoden besteht allerdings darin, dass das Zusammenspiel dieser Methoden auf die betriebsspezifischen Anforderungen ständig neu abzustimmen und zu hinterfragen ist. So unterliegt z.B. das Toyota-Produktionssystem, in dem bis heute die beschriebenen Methoden zur Anwendung kommen, seit mehr als 50 Jahren einem ständigen Lern- und Verbesserungsprozess. Auch nachdem 1960 die ersten Grundsätze, Elemente und Methoden des Produktionssystems in den Fabriken Toyotas eingeführt waren, suchte Toyota weiterhin nach Verbesserungspotenzialen, um die Produktivität zu steigern. Dies geschah und geschieht auch in den administrativen Bereichen. So wurden in den folgenden Jahren verschiedene weitere Elemente und Methoden entwickelt, die einander ergänzten und so das Räderwerk eines umfassenden aufeinander abgestimmten Produktionssystems entstehen ließen.